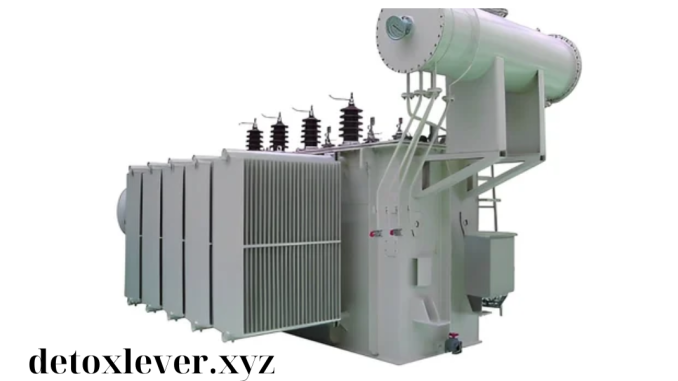
Introduction
For decades, oil-cooled transformers have been essential in the power industry, providing reliable performance and improved cooling for high-voltage applications. With rising demand for efficient and robust transformers, these units have proven invaluable in both distribution and power systems, making them crucial for various industries and energy grids worldwide. These transformers ensure stable power transmission by effectively handling high loads and dissipating heat, which is vital for maintaining continuous operation and preventing system failures.
In addition to their cooling capabilities, these transformers offer enhanced durability, minimizing the risk of wear and tear under heavy usage. As global infrastructure expands, they play a significant role in supporting renewable energy projects, industrial facilities, and public utilities. The adoption of oil-based cooling systems across industries highlights their reliability, as they efficiently manage the high energy demands of both traditional and emerging sectors. This versatility and resilience make oil-cooled transformers a backbone in modern power networks, ensuring safe, efficient, and sustainable energy distribution for decades to come.
Understanding Oil-Cooled Transformers
An oil-cooled transformer is a type of electrical transformer that uses insulating oil as both a cooling and insulating medium. Unlike dry-type models, these transformers are enclosed, with specialized oils filling internal spaces to keep the temperature optimal while insulating critical components. This setup ensures the transformer can operate under heavy loads and maintain high performance.
Key Components of Oil-Cooled Transformers
- Core: Acts as the transformer’s center, transferring energy between primary and secondary coils.
- Windings: Coils that transfer electrical energy within the transformer.
- Insulating Oil: This specialized oil dissipates heat and serves as an electrical insulator.
- Cooling System: Typically includes radiators or fans to dissipate heat and stabilize temperatures.
The Role of Oil in Transformer Operation
The oil within these transformers serves two essential functions:
- Cooling: As transformers operate, they generate heat due to electrical resistance. The oil absorbs this heat and transfers it to external cooling surfaces, preventing overheating.
- Insulation: The oil creates a non-conductive environment between internal components, reducing the risk of short circuits and allowing stable operation even under heavy loads.
Advantages of Oil-Cooled Transformers
Routine maintenance is essential to ensure safety, reliability, and peak performance in oil-cooled systems. Proactive attention to key areas of the transformer helps prevent costly repairs, reduces downtime, and extends the lifespan of the equipment. Here are several critical maintenance practices:
1. Oil Testing and Analysis
Periodic testing of the oil is crucial for detecting impurities and assessing the dielectric strength of the insulating liquid. Over time, contaminants such as moisture, acids, and other particulate matter can accumulate in the oil due to prolonged exposure to environmental factors and electrical stresses. Regular analysis helps in early detection of degradation and contamination, which, if unaddressed, could lead to reduced insulation effectiveness and potential equipment failures. By identifying these issues early, technicians can take preventive action to avoid serious operational disruptions.
2. Cooling System Maintenance
A fully functional cooling system is essential to managing internal temperatures, especially in high-load applications. Heat dissipation components, such as radiators, cooling fans, and oil pumps, should be routinely inspected for any blockages, wear, or mechanical failures. Malfunctioning cooling parts can lead to overheating, which strains the system and impacts both efficiency and longevity. Regularly scheduled checks ensure that cooling elements operate optimally, maintaining the system’s ability to handle high voltages and continuous operation without overheating.
3. Inspection of Seals, Gaskets, and Fittings
The seals and gaskets in these transformers play a vital role in maintaining the integrity of the oil enclosure. Any leaks in these components can lead to a loss of insulating oil, which compromises both the cooling and insulating properties of the transformer. Regular inspection of seals, gaskets, and fittings can help detect early signs of wear, cracks, or loosening that could lead to leaks. By promptly addressing these small issues, operators can avoid larger problems, such as oil contamination or reduced insulating capabilities, which might lead to inefficient performance or unsafe operating conditions.
Common Applications
Oil-cooled transformers are widely used across various sectors, including:
- Power Distribution: Essential for distributing electricity from generation stations to residential and commercial areas.
- Industrial Facilities: Industries with significant energy requirements rely on these transformers for consistent high-voltage power.
- Renewable Energy: Solar and wind power stations employ oil-cooled transformers to effectively manage and distribute generated power.
Maintenance and Safety for Oil-Cooled Transformers
Routine maintenance is essential to ensure safety and performance. Important maintenance practices include:
1. Oil Testing and Analysis
Regular oil testing helps detect contaminants and assess dielectric strength. Over time, insulating oil can degrade due to exposure to heat, moisture, and electrical stress. Testing ensures early detection of potential issues.
2. Cooling System Maintenance
A functioning cooling system is vital for effective heat dissipation. Regular inspection of radiators, fans, and pumps helps avoid overheating and equipment failure.
3. Inspection of Seals and Gaskets
Leaks can compromise both cooling and insulating properties. Routine inspection of seals and gaskets prevents leaks, ensuring safe and efficient operation.
Types of Oils Used
Various types of oils are used in these transformers, each suited for different needs:
- Mineral Oil: The most common choice, offering cost-effectiveness and excellent insulating properties.
- Silicone-Based Oils: Known for high flash points and lower environmental impact, suitable for indoor transformers.
- Biodegradable Oils: Eco-friendly options often used in regions with stringent environmental regulations.
The choice of oil depends on factors such as cost, environmental considerations, and specific application requirements.
Environmental Considerations
Oil-cooled transformers come with environmental considerations. Spills or leaks can affect soil and water sources. To minimize risks, companies often use secondary containment and eco-friendly oils, with regular monitoring and quick response mechanisms to reduce potential impact.
Choosing Biodegradable Oils
Some companies are turning to biodegradable oils as a more sustainable alternative. These oils break down faster than mineral oils, reducing the risk of long-term contamination.
Comparison with Dry-Type Transformers
Oil-cooled transformers are often compared with dry-type models, which are used in different environments. Here’s a quick comparison:
Feature | Oil-Cooled Transformers | Dry-Type Transformers |
---|---|---|
Cooling Method | Oil-based, effective for high loads | Air-based, suitable for lower loads |
Power Capacity | Ideal for high-power applications | Generally handles lower power loads |
Maintenance | Requires regular oil and cooling checks | Minimal maintenance, no oil needed |
Environmental Impact | Potential for spills, requires containment | Lower environmental risk |
Emerging Trends
With advancements in transformer technology, oil-cooled transformers are also evolving. Key trends include:
- Synthetic and Eco-Friendly Oils: Rising environmental awareness is leading manufacturers to develop alternatives to traditional mineral oils.
- Enhanced Monitoring Systems: Modern transformers are equipped with IoT-based systems for real-time monitoring of oil levels, temperature, and more.
- Compact Designs: Improved insulation and cooling technologies allow for more compact designs, ideal for high-density settings without compromising performance.
Conclusion
Oil-cooled transformers remain pivotal in the power industry, delivering unmatched efficiency, dependability, and extended service life across diverse high-demand applications. Their impact is evident in everything from power distribution grids to large-scale industrial operations, where they ensure a continuous, stable flow of electricity. While environmental factors, such as potential oil leaks or spills, require attention, manufacturers are actively improving oil compositions and containment strategies, advancing these transformers as an environmentally conscious and practical solution for modern power systems.
The future of oil-based cooling systems in transformers looks promising, especially as technology progresses with innovations like synthetic oils and smart monitoring. With their robust cooling capabilities, impressive power-handling capacity, and resilient structure, these transformers will likely remain the preferred choice for high-power applications in both traditional and renewable energy sectors.
Leave a Reply