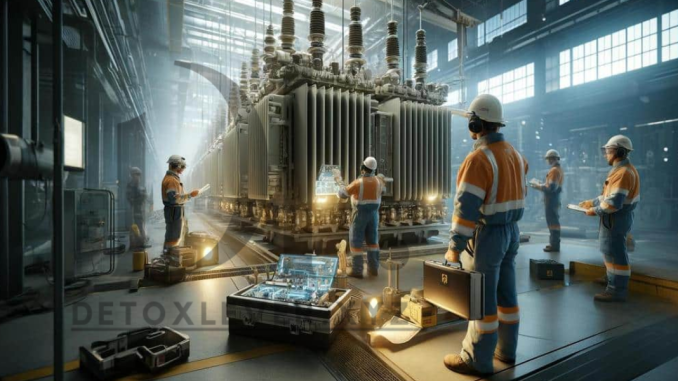
Transformers play a crucial role in electrical systems, enabling the smooth transmission of electricity across various devices and utilities. They are used in both residential and industrial settings, ensuring the right voltage levels are delivered for diverse applications. Ensuring that transformers are properly maintained is vital for maximizing their lifespan, enhancing operational efficiency, and preventing costly repairs. Without proper care, transformers can experience issues like overheating, electrical faults, or even complete failure, which can lead to extensive downtime and significant repair costs. In this comprehensive guide, we will explore essential transformer maintenance tips that can help you keep your equipment in top condition, ensuring that it continues to perform at optimal levels for years to come.
Why Transformer Maintenance is Important
Transformers are essential for converting voltage from high to low levels, making them vital for the distribution of power. Whether they are used for step-up or step-down transformations, transformers are involved in nearly every electrical operation. Over time, however, their components may deteriorate, affecting their efficiency. Regular transformer maintenance is necessary to detect early signs of wear and tear before they evolve into larger, more expensive problems. Neglecting maintenance can result in premature failure, leading to system downtime, costly repairs, and even safety hazards. Scheduled care ensures the transformers run efficiently, prolonging their useful life and preventing costly emergency repairs.
Transformers have a wide range of applications in industries such as power generation, telecommunications, and manufacturing, where they are critical for both power supply and system stability. This makes the maintenance of transformers even more important, as any disruption in power flow can cause significant damage, financial loss, and potentially harm equipment connected to the transformer.
1. Regular Visual Inspections
A visual inspection is one of the simplest yet most effective maintenance techniques. Visual checks can identify problems before they become more severe, such as leaks, corrosion, and overheating. During these inspections, check for visible signs of wear, such as:
- Oil leaks: Leaking oil can indicate internal damage or that the seals are deteriorating, potentially leading to poor cooling and increased risk of fire.
- Corrosion: Rust can affect the transformer’s housing and internal components, leading to further degradation. Regularly inspecting for signs of corrosion can help you address issues early.
- Buildup of dirt or debris: Accumulation of dust, leaves, or other materials can obstruct ventilation, leading to overheating and possible failure of the unit.
Routine checks every 3-6 months allow early detection of potential problems and ensure your transformer operates smoothly. In some environments, frequent checks may be necessary depending on the conditions, such as extreme weather or high moisture.
2. Maintain Transformer Oil Levels and Quality
For oil-filled transformers, the oil serves as both a coolant and an insulator. Transformer oil helps prevent overheating by dissipating heat from the winding and core. Over time, transformer oil can degrade, losing its insulating properties. Therefore, maintaining proper oil levels and quality is essential for preventing overheating and ensuring efficient heat dissipation. Here are some important steps:
- Check oil levels regularly: Low oil levels can lead to inadequate cooling, risking overheating. Ensure that oil levels are within the recommended range.
- Oil testing: Periodically sample the oil to check for contamination, acidity, and breakdown of insulating properties. If the oil shows signs of deterioration, it should be replaced to avoid damaging the transformer’s internal components.
Proper oil maintenance can extend the life of your transformer, reduce the likelihood of costly repairs, and ensure continuous, safe operation.
3. Monitor and Clean Cooling Systems
Cooling systems are integral to maintaining a transformer’s temperature within safe limits. A cooling failure can lead to transformer damage, overheating, and inefficiency. Whether your transformer uses air or oil as a coolant, dirt and debris can impede airflow, causing excessive heat buildup. To avoid this, clean cooling fans, vents, and heat exchangers regularly. Cooling system maintenance should include:
- Cleaning fans: Dust and debris can block cooling fans, reducing airflow.
- Checking vents and heat exchangers: Ensure that no debris or dirt accumulates in these areas. Even small obstructions can cause a significant rise in temperature.
Regular cleaning and maintenance of the cooling system ensure that the transformer’s temperature remains stable, preventing overheating and system failures. If the cooling system is malfunctioning, it could lead to a transformer failure, even if the transformer itself is functioning normally.
4. Inspect and Tighten Electrical Connections
Loose or damaged electrical connections can lead to overheating, voltage imbalances, and potential transformer failures. This is one of the most common causes of transformer malfunctions. During your maintenance routine, inspect both the primary and secondary electrical connections to ensure they are tight and secure. Look for signs of overheating, such as burnt or discolored terminals. Here’s how to maintain secure connections:
- Tighten connections: If any connections appear loose, tighten them using the proper torque. Loose connections can lead to resistance buildup, which causes overheating.
- Inspect cables for wear: Cables can become damaged over time due to vibration or external environmental factors. Replace worn cables immediately to avoid power loss or failure.
By ensuring the electrical connections are intact, you improve the transformer’s reliability and reduce the risk of malfunctions or dangerous situations like short circuits.
5. Perform Insulation Resistance Testing
Over time, the insulation on a transformer’s windings can degrade due to environmental factors like moisture, heat, and vibration. Insulation resistance testing helps detect issues with the insulation early on, preventing the risk of short circuits or equipment failure. Using a megger or insulation resistance tester, measure the resistance of the transformer’s insulation.
- Low resistance readings: If the readings are lower than the recommended levels, it may indicate deterioration of the insulation. In such cases, the insulation needs to be replaced or repaired.
- Moisture detection: Insulation resistance tests can also reveal the presence of moisture, which can significantly affect the transformer’s performance and longevity.
Periodic insulation testing is a key part of transformer maintenance as it helps detect potential issues before they lead to catastrophic failure.
6. Check for Overload Conditions
An overloaded transformer operates under excessive stress, which can lead to overheating and reduced efficiency. During maintenance checks, ensure that the load on the transformer is within the rated capacity. If the transformer is continuously operating near or beyond its limits, it could significantly shorten its lifespan.
- Use load monitoring tools: These tools help track the transformer’s operational parameters, ensuring it is not operating beyond its rated capacity.
- Proper load balancing: Ensure that the transformer is not overloaded and that the load is evenly distributed across the system.
By avoiding overload conditions, you can prevent unnecessary strain on the transformer, ensuring its longevity and reducing the risk of unexpected breakdowns.
7. Keep Transformer Relays and Circuit Breakers in Check
Protective relays and circuit breakers are vital safety mechanisms that disconnect the transformer from the grid in the event of a fault. Regularly test these devices to ensure they are functioning correctly and will activate when needed. Faults such as short circuits, overloads, or other electrical issues can damage the transformer if the relays or circuit breakers do not engage in time.
- Test settings and calibration: Periodically check the settings of your protection devices to ensure they are correctly calibrated for your system’s needs.
- Modern protection devices: Consider installing advanced protection devices with diagnostic capabilities that offer enhanced monitoring and help prevent transformer failure.
Well-maintained relays and circuit breakers play a crucial role in protecting transformers from faults and ensuring the reliability of your electrical system.
Conclusion
Proper transformer maintenance is critical to maximizing the lifespan, efficiency, and reliability of your equipment. By following these expert maintenance tips, you can reduce the likelihood of unexpected failures, enhance performance, and save on costly repairs. Regular inspections, oil management, electrical connection checks, and proactive load monitoring are just some of the steps that help keep transformers running smoothly.
Don’t forget to rely on professional services for more complex maintenance and diagnostics. Experienced technicians can conduct advanced tests such as thermal imaging and partial discharge testing, which may uncover issues that routine checks could miss. With consistent care and regular professional inspections, your transformer will continue to function optimally, contributing to the long-term success of your electrical system.
Maintaining transformers effectively not only helps extend their service life but also ensures the uninterrupted operation of your business or facility. When properly maintained, transformers become a reliable and efficient part of your infrastructure, saving you time, money, and potential headaches.
Leave a Reply